rockwell hardness test on curved samples|rockwell hardness testing procedure pdf : maker The Rockwell hardness number used to evaluate a sample is calculated based on the depth of permanent deformation into the sample, or . Login to XvideosOnlyFans - OnlyFans Grátis, Privacy Grátis, Close Friends Vazados, Xvideos
{plog:ftitle_list}
1. Discrete Probability Distributions. 1.1 An Introduction to Dis.
rockwell hardness testing procedure pdf
Foremost to any Rockwell test process is identification of the proper hardness scale to be used on the component to be tested. There are 30 different Rockwell scales with the majority of applications covered by the .If a Rockwell test is conducted on cylindrical parts, then, due to the lower resistance of the test surface with respect to the indenter, the following correction values – depending on the . The Rockwell hardness number used to evaluate a sample is calculated based on the depth of permanent deformation into the sample, or .
The Rockwell hardness test at a glance: Generally used for larger samples. No optical readout. Can be used for advanced tests. Standards: ASTM E18, ISO 6508 and JIS Z 2245. See our complete range of Rockwell hardness testing .
The Rockwell hardness test measures the depth of penetra-tion of an indenter into a material under a known load. It provides a hardness value based on the depth of penetration. 2 Brinell .
The Rockwell test is based on measurement of the depth of penetration with the hardness number read directly from the dial gauge or digital display that is part of every tester. In . for testing hardness in plastics, like Shore (Durometer), Rockwell, the Ball indentation hardness test and Barcol. This Application Note will focus on hard-ness testing . The purpose of this Guide is to explain the causes of variability in Rockwell hardness test results and to supplenment the information given in test method standards with .
By utilizing a few “best practices” in hardness testing such as closed-loop load monitoring, the appropriate preparation for test samples, repeated sample measurements, and adjusting measured values for gage bias, measurement .
The Rockwell hardness test method, as defined in ASTM E-18, is the most commonly used hardness test method. You should obtain a copy of this standard, read and understand the standard completely before attempting a .What is Rockwell hardness testing? The Rockwell Hardness Test is generally a non-destructive test performed on samples when it’s necessary to determine how hard a material is. It’s generally considered easier to perform compared .
If a Rockwell test is conducted on cylindrical parts, then, due to the lower resistance of the test surface with respect to the indenter, the following correction values – depending on the specimen curvature radius and the Rockwell scale used – must .The Rockwell Hardness Test. . Place the test sample on the anvil. 3. A preliminary test force (commonly referred to as preload or minor load) is applied to a sample using a diamond indenter. . The Brinell hardness number is a function of the test force divided by the curved surface area of the indent. The indentation is considered to be .Hardness testing is key in most quality control procedures. That’s why we provide a complete range of hardness testing equipment and accessories for every need, from small lab applications to heavy-duty hardness testing in production. Check out our range of hardness testing equipment to ensure your equipment is up to the task. See our .The Rockwell hardness testing method fulfilled every requirement. After 100 years, it’s still the best metal strength test method. The Rockwell C scale is also the most precise way to report metal strength used in industrial machine knives. How Rockwell Hardness Gets Measured.
Rockwell Hardness Testing Reference Guide ASTM E18 contains a listing of all regular Rockwell scales and typical materials for which these scales are applicable. Use these tables in selecting the scale that is appropriate for your application. Regular Rockwell Testing. In this test method, the minor (preload) is always 10 kgf. .Portable Rockwell hardness testers are available, which allow for on-site or field hardness testing. This is advanta-geous for applications where it is not feasible to transport samples to a laboratory or for situations that require imme-diate hardness assessment. Portable Testing 1.1
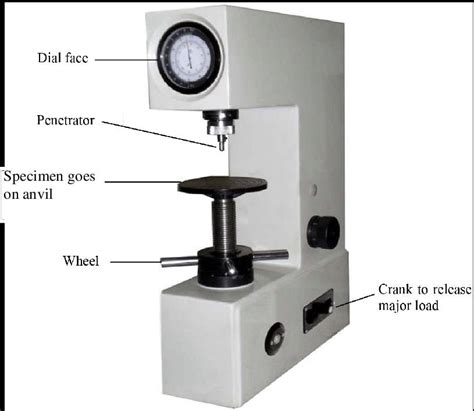
rockwell hardness testing guide pdf
The Rockwell Hardness test is a widely used method to determine the hardness of metallic materials, thanks to its simplicity and quickness. This hardness test is based on indentation and depth of penetration, and it can be performed on various metals, including aluminum, copper alloys, brass, soft steels, and hard carbon steels.Test pieces that are not flat should be placed on the spot anvil with the curved side down to ensure that solid contact is made with the anvil at the point of test. . Verification should be performed by an accredited verifying agency and the report should follow and reference ASTM E18 Rockwell test method. Hardness testing is an important and .Hardness testing within the realm of materials testing. Today, hardness testing is one of the most widely used methods in mechanical materials testing, especially for metals. On the one hand, this test method can be used to find qualitative relations to other material properties (e.g., strength, stiffness, density) or to the material behavior under certain stresses (e.g., abrasion . Defining Correction Factors. ASTM Standard E18 also has tables for defining correction factors when testing cylindrical shapes (see Figure 2).The corrections vary according to the sample's diameter and hardness and can be as much as six points on the HRC scale and 12.5 points on the HRB scale.
Test pieces that are not flat should be placed on the spot anvil with the curved side down to ensure that solid contact is made with the anvil at the point of test. . Verification should be performed by an accredited verifying agency and the report should follow and reference ASTM E18 Rockwell test method. Hardness testing is an important and .
Best Practices for Rockwell Hardness Testing Hardness Testing Basics Hardness, as applied to most materials, and in particular metals, is a valuable, revealing, and commonly employed mechanical test that has been in use in various forms for more than 250 years. As a material property, its value and importance cannot be understated; the information The Rockwell hardness test continues to be applied as a tool for assessing the properites of a product while the tolerances on the acceptable material hardness have become tighter and tighter. Adhering to good practice procedures when performing Rockwell hardness measurements and calibrations is a beneficial step to reducing measurement errors.When the sample surface is curved, it is necessary to measure the length of the diagonal of the indentation on the curved surface correctly. ISO 6507-1 and . example of a Vickers hardness test of curved surfaces. C. Oya Hardness Correction Factors in Tests of Curved Surfaces (ISO 6507-1, JIS Z 2244)See also: Hardness. Rockwell Hardness Test. Rockwell hardness test is one of the most common indentation hardness tests, that has been developed for hardness testing. In contrast to Brinell test, the Rockwell tester measures the depth of penetration of an indenter under a large load (major load) compared to the penetration made by a preload .
The Rockwell hardness test is based on the difference of indenter depth from two load . Mounted samples that rely on the mounting material to provide the support surface . 2. Curved test surfaces must be aligned so that deformation will be uniform on Although the polishing method used for sample group 1 produces what seems to be a high-quality surface finish, it leaves a significant amount of deformed metal near the surface of the component, which results in erroneous and misleading hardness-testing results. Sample group 2, by contrast, displayed only marginally higher hardness values than .
The Rockwell hardness test method, as defined in ASTM E-18, . Another special case when testing cold-rolled sheet steel is that hardening can create a gradient of hardness through the sample, so each test measures the average of the hardness over the depth of indentation. In this case, any Rockwell test result will be subject to doubt because . The next decision is to select the correct Rockwell hardness scale to conduct the tests. Please review ASTM E18 for proper selection based on case depth and size of the sample—usually, the smaller the sample, the lighter the load to be used. The Rockwell test is probably the most common hardness test used in industry today.A Rockwell hardness tester. The Rockwell scale is a hardness scale based on indentation hardness of a material. The Rockwell test measures the depth of penetration of an indenter under a large load (major load) compared to the penetration made by a preload (minor load). [1] There are different scales, denoted by a single letter, that use different loads or indenters.
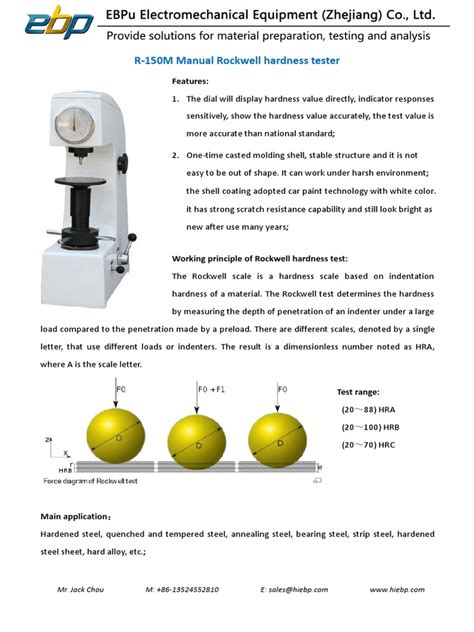
Test pieces that are not flat should be placed on the spot anvil with the curved side down to ensure that solid contact is made with the anvil at the point of test. . Verification should be performed by an accredited verifying agency and the report should follow and reference ASTM E18 Rockwell test method. Hardness testing is an important and .
The Rockwell hardness test is the industry standard measuring system used to determine how resistant a material is to another object. Hardness is defined as a material’s resistance to permanent indentation. This test was created to determine the hardness and strength of materials. After executing the Rockwell hardness test, you will be able .
And the most common of these verification methods, employed by forgers of steel, aluminum, and titanium, is Rockwell Hardness testing. (See Figure 1.) The general principle of Rockwell testing, as defined by ASTM E18 1, is relatively simple: A hardened indenter made to a specific geometry is brought into contact with the test piece. The Rockwell hardness test involves applying a sequence of loads to the material and measuring the depth of the resulting indentation, which indicates the material’s hardness. . Sample preparation: Ensure that the sample surface is properly prepared, free of contaminants, and has a smooth, flat surface. Inconsistent surface conditions can .ISO 6508-3:2015, Metallic materials — Rockwell hardness test — Part 3: Calibration of reference blocks 3 Principle An indenter of specified size, shape, and material is forced into the surface of a test specimen under two force levels using the specific conditions defined in Clause 7. The specified preliminary force is applied
Paulo³³. 26 anos. R$ 130/h. 1. 2. Lindas acompanhantes em Cabo Frio, as mais belas acompanhantes de luxo na cidade de Cabo Frio. Confira todas as garotas de programa de Cabo Frio.
rockwell hardness test on curved samples|rockwell hardness testing procedure pdf